The Ultimate Guide to Choosing the Right Packaging Machine Repair Experts
The Ultimate Guide to Choosing the Right Packaging Machine Repair Experts
Blog Article
Quick and Reliable Packaging Maker Fixing Solutions to Decrease Downtime
In the affordable landscape of production, the effectiveness of product packaging procedures depends upon the dependability of equipment. Quick and reliable repair service solutions are vital in alleviating downtime, which can lead to substantial functional problems and economic losses. Comprehending the relevance of prompt treatments and the role of expert specialists can transform just how services approach repair and maintenance. Nonetheless, navigating the myriad alternatives available for repair service solutions can be difficult. What aspects should businesses think about to guarantee they are making the best selection for their operational demands?
Importance of Timely Fixes
Prompt repair services of packaging machines are important for keeping functional effectiveness and decreasing downtime. In the fast-paced setting of manufacturing and packaging, also minor breakdowns can cause significant delays and productivity losses. Addressing concerns quickly makes certain that equipments operate at their ideal capability, consequently protecting the circulation of procedures.
Furthermore, prompt and regular upkeep can stop the escalation of small issues right into major break downs, which commonly incur higher repair prices and longer downtimes. A proactive method to maker fixing not only maintains the integrity of the equipment but likewise boosts the overall reliability of the assembly line.
Furthermore, timely fixings add to the durability of product packaging machinery. Devices that are serviced promptly are less most likely to endure from excessive deterioration, allowing companies to maximize their investments. This is specifically crucial in markets where high-speed packaging is essential, as the requirement for consistent efficiency is paramount.
Benefits of Reliable Solution Companies
Trustworthy service suppliers play an essential function in making sure the smooth operation of packaging devices. Their knowledge not just enhances the efficiency of fixings but likewise adds significantly to the long life of tools.
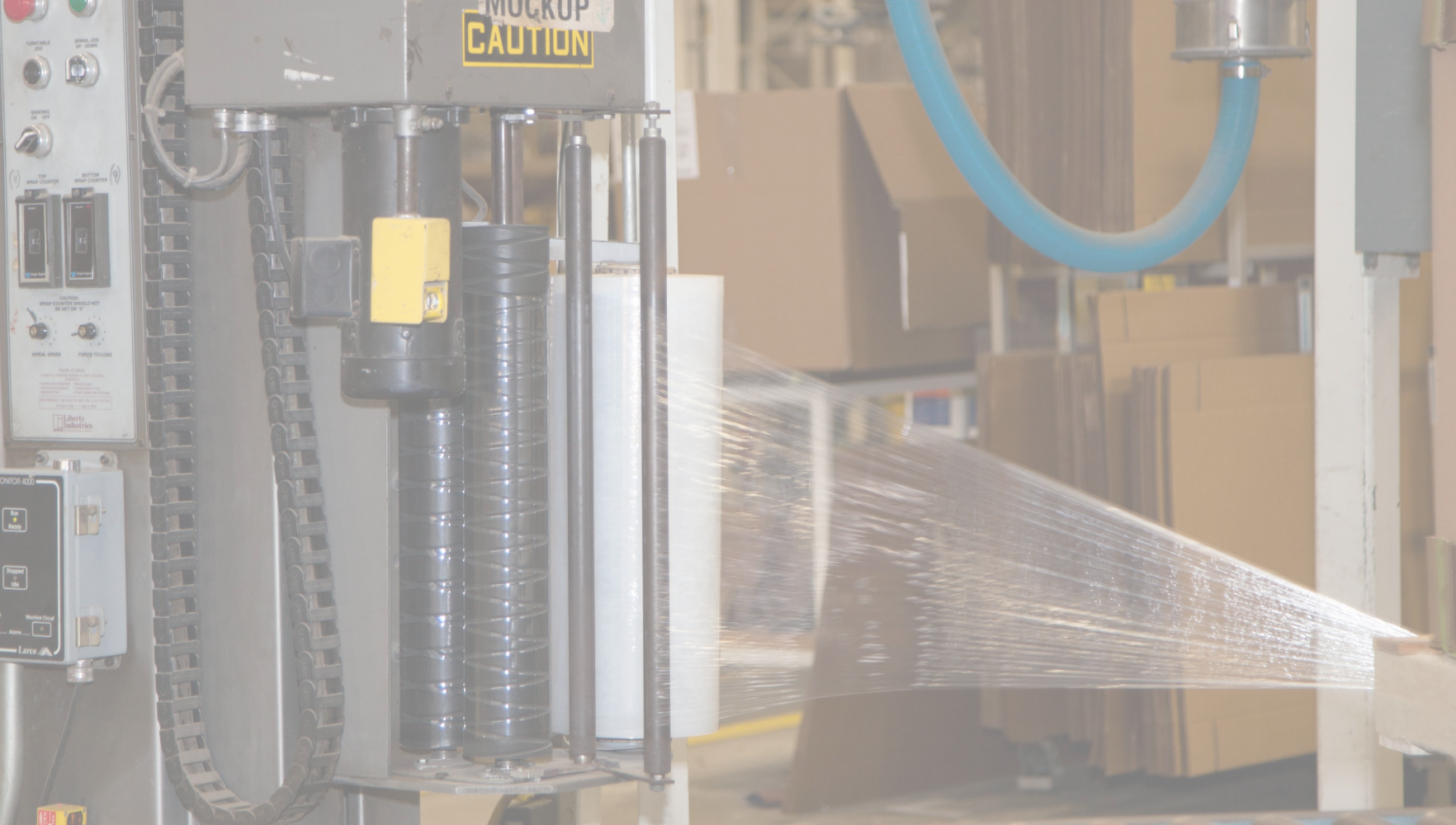
In addition, a reputable provider uses extensive support, consisting of training and support for team on machine procedure and upkeep best methods. This not only encourages employees however likewise cultivates a society of security and efficiency within the company. Generally, the benefits of involving dependable service providers prolong past immediate repairs, favorably impacting the entire operational process of product packaging processes.
Typical Product Packaging Equipment Concerns
In the realm of product packaging operations, numerous problems can endanger the efficiency and performance of machines (packaging machine repair). Another common issue is misalignment, which can trigger jams and unequal product packaging, impacting product quality and throughput.
Electrical problems can also interrupt product packaging procedures. Malfunctioning circuitry or malfunctioning sensing units may result in unpredictable machine behavior, creating delays and raised functional prices. Additionally, software application glitches can impede the equipment's programming, causing functional ineffectiveness.
Inconsistent product flow is one more essential concern. This can occur from variants in product form, weight, or size, which might impact the maker's ability to deal with products properly. Not enough training of drivers can worsen these troubles, as inexperienced workers might not identify early indicators of malfunction or may abuse the devices.
Resolving these typical packaging maker problems quickly is vital to keeping productivity and making certain a smooth procedure. Normal inspections and positive upkeep can substantially mitigate these issues, promoting a trustworthy packaging atmosphere.
Tips for Reducing Downtime
To reduce downtime in product packaging operations, carrying out a positive upkeep strategy is important. Routinely set up upkeep checks can identify possible issues prior to they escalate, ensuring equipments operate efficiently. Establishing a regimen that consists of lubrication, calibration, and examination of crucial parts can dramatically minimize the regularity of unforeseen breakdowns.
Educating personnel to operate machinery properly and acknowledge early indication of malfunction can likewise play an important function. Equipping drivers with the expertise to perform fundamental troubleshooting can avoid minor problems from creating major delays. In addition, preserving an efficient supply of important extra components can accelerate repair services, as waiting on components can bring about prolonged downtime.
In addition, documenting maker performance and maintenance tasks can help recognize patterns and recurrent problems, enabling targeted interventions. Incorporating sophisticated surveillance innovations can give real-time information, enabling anticipating maintenance and minimizing the threat of abrupt failures.
Last but not least, cultivating open communication between drivers and maintenance groups guarantees that any irregularities are without delay reported and attended to. By taking these aggressive steps, businesses can boost functional efficiency and considerably decrease downtime in packaging processes.
Choosing the Right Fixing Service
Choosing the suitable fixing solution for straight from the source packaging devices is an essential choice that can considerably impact functional performance. A well-chosen provider guarantees that your equipment is fixed promptly, efficiently, and to the greatest criteria. Begin by assessing the service provider's experience with your specific sort of packaging equipment. A specialist knowledgeable about your machinery can detect concerns much more accurately and apply options a lot more rapidly.
Next, think about the company's online reputation. Looking for responses from other organizations within your industry can supply insights into reliability and high quality. Accreditations and collaborations with identified equipment producers can likewise indicate a dedication visit this web-site to excellence.
Furthermore, analyze their reaction time and accessibility. A company who can provide timely assistance decreases downtime and maintains production circulation steady. It's also vital to ask about service warranty and solution guarantees, which can reflect the confidence the supplier has in like this their work.

Conclusion
To conclude, the relevance of trusted and fast product packaging machine fixing solutions can not be overstated, as they play a vital duty in reducing downtime and guaranteeing functional performance. By prioritizing prompt repair work and selecting reliable company, services can efficiently keep and resolve typical problems efficiency. Carrying out proactive upkeep practices and investing in personnel training additional improves the longevity of product packaging equipment. Eventually, a calculated approach to repair services cultivates an extra durable production atmosphere.
Timely fixings of packaging machines are critical for maintaining functional effectiveness and lessening downtime.Furthermore, prompt repair work contribute to the durability of packaging machinery. Overall, the advantages of involving reputable solution suppliers expand past prompt repairs, favorably influencing the entire functional process of packaging processes.
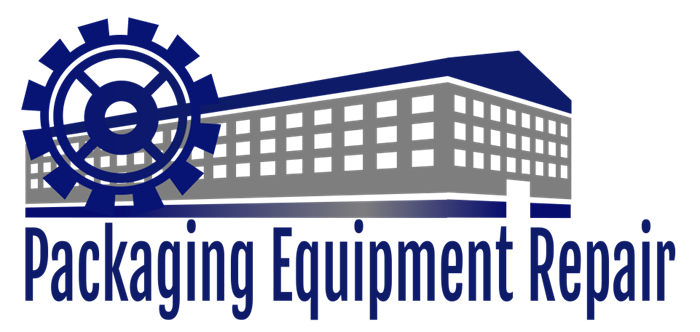
Report this page